Il TNT è particolarmente presente nelle nostre vite in queste settimane. Sono realizzati in tessuto non tessuto molti dispositivi medici e di protezione individuale (DPI) così necessari durante l’emergenza coronavirus. Ma questo materiale è molto più diffuso di quanto crediamo, ogni giorno e in settori molto diversi.
Il TNT è un materiale diffusissimo: nel 2018 ne sono stati prodotti in tutto il mondo 14,9 milioni di tonnellate (fonte: EDANA). È impiegato nei settori più disparati e “insospettabili”, come l’ingegneria civile o la manifattura industriale. Oltre che per le sue caratteristiche fisiche e chimiche, che peraltro variano e di molto a seconda delle materie prime, viene apprezzato per la sua capacità di essere prodotto in grandi quantità (una sola fabbrica può produrre anche più di 3.000 chili di TNT l’ora) a costi contenuti. Ma ha anche alcuni punti deboli, che devono assolutamente essere tenuti in considerazione: il principale è la sua scarsa resistenza meccanica. Per questo viene usato soprattutto come materiale usa e getta.
Conoscere le caratteristiche chimiche, fisiche e meccaniche dei TNT ti aiuterà a scegliere in maniera più consapevole i materiali da stampare. Come sempre, tieni a mente alcune domande-guida:
- Qual è la destinazione d’uso del prodotto finito?
- Dove verrà usato fisicamente il prodotto finito?
- Che resistenze sono necessarie?
- Quali lavorazioni sono necessarie per arrivare al prodotto finito?
- Quali tecniche di decorazione posso usare?
Non tutti i tessuti non tessuti vengono stampati: anzi, sono solo una piccola parte quelli che hanno la dignità di essere visti. Molti, se anche vengono stampati o decorati in qualche modo, hanno una destinazione d’uso funzionale e non decorativa o comunicativa. Ma bisogna anche ricordare che sono numerosi i materiali usati nel settore della visual communication che hanno un’anima in TNT: non viene stampato direttamente il tessuto non tessuto, ma il materiale che lo ricopre.
È quindi necessario circoscrivere l’argomento: in questo articolo parleremo dei TNT in generale, ma ci focalizzeremo su quelli che sono effettivamente stampati (o almeno stampabili) direttamente.
Agugliatura o needle punching: processo con cui si compatta il materasso di fibre uscito dalla carda, attraverso aghi in metallo che si muovono in verticale.
Agugliatura ad acqua, hydroentanglement o spunlace: processo di coesione del materasso di fibre simile all’agugliatura tradizionale, realizzata tramite getti d’acqua ad alta pressione.
Artificiale: materiale creato a partire da materiali naturali, elaborati attraverso un processo chimico.
Cardatura: processo che assottiglia e raddrizza la massa di fibre tessili passandole in una “carda”, una macchina composta da due rulli muniti di dentini in metallo.
Decitex (dtex): unità di misura della densità lineare di un filo o filato, comunemente usata in ambito tessile; corrisponde al peso in grammi di 10 km di filo.
Denaro (den): unità di misura della densità lineare di un filo o filato, comunemente usata in ambito tessile; corrisponde al peso in grammi di 9 km di materiale.
Densità o finezza: unità di misura del TNT; misura la quantità di fibra per centimetro quadrato (fibra/inch²).
Fibre tessili: prodotti fibrosi naturali, sintetici o artificiali che possono essere trasformati in filati e tessuti. Possono essere discontinue, in inglese staple fiber (che nel caso in cui vengano filate danno origine a filati), oppure continue (fili).
Filo: materiale composto da una fibra continua. L’unico filo naturale è la seta; gli altri sono di origine artificiale o sintetica.
Filato: materiale composto da fibre corte, filate insieme. Sono filati la lana, il cotone, la canapa, ma possono esserlo anche materiali sintetici e artificiali.
Finezza: v. densità.
Finissaggio: processo chimico, fisico o meccanico che agisce sull’aspetto e sulle resistenze di un filo, un filato, un tessuto.
Idrofobia o idrofobicità: proprietà di un materiale di non assorbire e non trattenere acqua né all’interno né sulla superficie.
Interlacciatura o coesionamento: tecnica che conferisce compattezza al materasso di fibre, dando origine al TNT senza usare la tessitura.
Mangano: macchina formata da tre cilindri ruotanti che comprimono il tessuto; la manganatura schiaccia il filato in modo da appiattirlo e chiudere gli interstizi.
Needle punching: v. agugliatura.
Ovatta: semilavorato di alcune lavorazioni tessili, costituito da un insieme disordinato di fibre; opportunamente trattata o sterilizzata viene usata nel settore sanitario, in sartoria e tappezzeria.
Sintetico: materiale creato a partire da materiali non naturali, attraverso un processo di sintesi chimica.
Spunlace: v. agugliatura ad acqua.
Termoplasticità: proprietà di un polimero acquistare plasticità (passando a uno stato viscoso, e quindi formabile), all’aumentare della temperatura, in modo reversibile.
Titolo: la finezza di un filo o un filato, ovvero la relazione tra lunghezza e peso. Per le fibre sintetiche è usata la titolazione diretta, che si misura in Decitex.
Through-air o thru-air bonding: tecnica di coesionatura della fibra che impiega aria calda.
TNT o tessuto non tessuto: prodotto industriale simile al tessuto, ottenuto però da procedimenti diversi rispetto alla tessitura e alla maglieria. Le fibre non sono disposte in modo ordinato, ma casuale.
Le materie prime
Oltre il 90% dei TNT è composto da fibre sintetiche (come il poliestere o il polipropilene) o artificiali (come la viscosa), ma i tessuti non tessuti possono essere fatti anche di fibre naturali (come il cotone o la lana). Nei settori che ci interessano (comunicazione visiva, food & beverage e igienico-medicale) sono le fibre sintetiche a farla da padrone, o al limite composizioni miste (per esempio, i fazzolettini igienici umidificati sono di viscosa e poliestere). I polimeri più usati per realizzare TNT sono il nylon, il polietilene, ma soprattutto il poliestere e il polipropilene – e proprio su questi ci concentriamo in questo articolo. Insieme costituiscono quasi il 90% delle fibre usate nel mercato (fonte: Nonwoven Textiles 1997-2007 World Survey, Tecnon).
Del poliestere (anzi, dei poliesteri) abbiamo già parlato nell’articolo Sai davvero cosa succede quando stampi il tessuto di poliestere?, sul numero 44 di WIDE, a cui ti rimandiamo per approfondimenti. Ma circa due terzi del TNT prodotto in tutto il mondo è in polipropilene (fonte: Nonwoven Textiles 1997-2007 World Survey, Tecnon): perché questo successo? Anche il polipropilene, noto anche come PP, è un polimero termoplastico, proprio come il poliestere. È il materiale di cui sono fatti moltissimi oggetti di uso quotidiano, dagli zerbini agli scolapasta, dalle etichette delle bottiglie di plastica alle custodie dei CD, dalle capsule per il caffè ai bicchieri bianchi usa e getta. È particolarmente apprezzato per produrre TNT per vari motivi: innanzitutto fonde a circa 160 °C, mentre il poliestere si deforma a temperature comprese tra i 225 e 240 °C, e questo rende più economici i processi di interlacciatura termici (li vediamo nel dettaglio più avanti). Inoltre ha una densità specifica inferiore a quella del poliestere: questo significa che un TNT in polipropilene, a parità di volume, sarà più leggero di uno in poliestere. Ha un’idrofobia intrinseca che può essere modificata con finissaggi in massa e superficiali. È anche stabile dal punto di vista chimico (non si deteriora); resiste al degrado biologico (muffa e sudore); non si sporca facilmente. Ha infine una buona resistenza meccanica e all’abrasione (v. Handbook of Nonwovens, 2007). Nel settore della comunicazione visiva vengono però spesso privilegiati i TNT in poliestere: questo perché è possibile stamparli anche in sublimazione (il polipropilene fonderebbe).
Igienico
Pannolini, tamponi e assorbenti; fazzoletti e salviette asciutti o umidificati (wipe); lenzuola usa e getta
Sanitario e medicale
Mascherine e camici; tamponi e materiale chirurgico; materiale per bendaggi e ingessature
Filtrazione (liquidi e gas)
Tè, liquidi; assorbimento di olio; filtri respiratori; filtri industriali
Biancheria per la casa
Tovaglie e tovaglioli; poggiatesta per mezzi di trasporto; biancheria da letto e federe; fodere; tendaggi
Arredamento
Moquette e piastrelle in moquette; tappeti per auto e moto
Edilizia
Pavimentazioni; tetti; isolamento termico e acustico
Costruzioni
Substrati nelle strade, nei terreni; sistemi di drenaggio dell’acqua
Manifatturiero
Supporti per spalmatura, accoppiatura, stampa: pelle sintetica, gomma
Comunicazione visiva
Banner, pettorali, borse, shopping
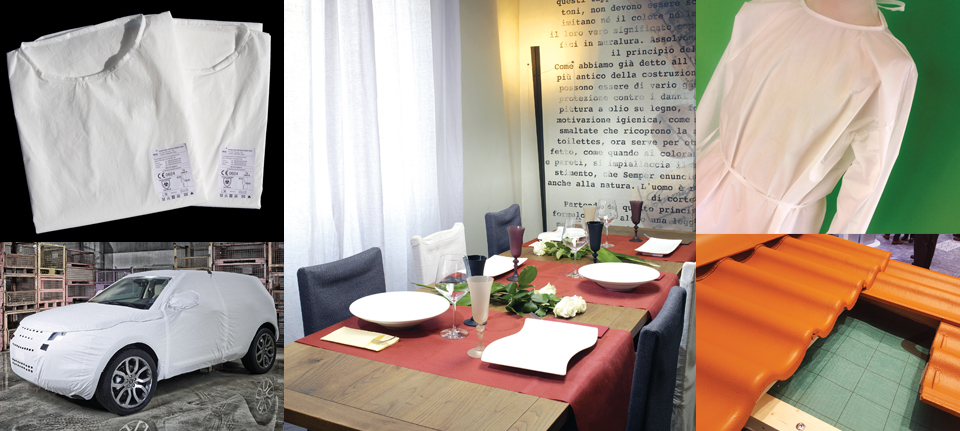
Il tessuto non tessuto è uno dei materiali più versatili e diffusi al mondo: viene usato nell’edilizia e nell’automotive, nel food e nella comunicazione visiva, nel medicale e nell’agricoltura. E non solo. Foto: RadiciGroup
Il deposito delle fibre continue e discontinue
I TNT in materiali sintetici e artificiali possono essere prodotti a partire da fibre discontinue o da fibre continue. Per capire un attimo le proporzioni: nel 2018 quasi il 60% del TNT è stato prodotto da fibre discontinue (fonte: EDANA). Nel caso della fibra discontinua il processo produttivo si svolge in due passaggi: prima vengono prodotte e tagliate le fibre, e poi si procede alla fabbricazione del TNT. Nel caso della fibra continua il processo produttivo è continuo: si parte dalla materia prima per arrivare direttamente al rotolo di prodotto finito.
La lavorazione della fibra discontinua
Ci sono diversi modi per trasformare una balla di fibra tessile discontinua in un velo pronto per essere interlacciato. Le tecniche di deposito sono: il dry-laid, ovvero una sorta di cardatura (come quella che viene fatta per la lana o il cotone), in cui le fibre vengono separate e direzionate; l’air-laid, che si può considerare in effetti un tipo di dry-laid, in cui le fibre vengono trasportate su un tamburo in modo pneumatico; e infine il wet-laid, in cui le fibre vengono trasportate da un getto d’acqua. In questi ultimi due casi (air-laid e wet-laid) le fibre vengono depositate in modo casuale, non hanno una direzione precisa.
La tecnica del dry-laid trae la sua origine dal mondo tessile, mentre quella del wet-laid dal mondo della carta (la cui tecnica produttiva in effetti presenta numerose analogie con quella del TNT). I TNT ottenuti tramite dry-laid costituiscono il segmento più ampio del mondo dei non tessuti.
Le fibre del materiale ottenuto possono essere disposte in modo random, a croce, oppure allineate longitudinalmente o trasversalmente. Se questo materiale non subisce ulteriori lavorazioni si definisce “ovatta”, e viene impiegato per esempio nel settore igienico-sanitario o in sartoria e tappezzeria.
La lavorazione della fibra continua
I TNT da fibra continua vengono prodotti in un unico passaggio, dalla materia prima al prodotto finito. Il processo produttivo è compatto ed economicamente conveniente. La tecnica di deposito delle fibre continue, sintetiche o artificiali, viene detta polymer-laid.
Si parte dai polimeri in forma di granuli (detti anche chip o pellet): vengono inseriti in un estrusore, un cilindro al cui interno gira una vite che mescola e fonde tutto il materiale. Al polimero possono essere aggiunti additivi che servono a modificarne alcune caratteristiche e proprietà: elasticità, idrorepellenza, resistenza al fuoco o alla luce. Il polimero fuso entra nella filiera, da cui escono fili molto sottili: pesano circa 2 o 3 denari e il loro diametro può andare dai 15 ai 25 micron. I fili prodotti hanno caratteristiche diverse a seconda di come vengono ottenuti; alcuni tipi di TNT prendono nome dal processo di estrusione dei fili da cui sono composti: i fili dello spunbond vengono semplicemente fusi; quelli del meltblown sono fusi e e per favorire l’indurimento passano attraverso un getto di gas ad alta velocità; quelli del flashspun cambiano composizione chimica a causa della rapida evaporazione del solvente proprio durante l’estrusione.
Per aumentarne la resistenza meccanica, i fili subiscono un processo di stiro che ne orienta le molecole. Lo stiro viene svolto con aria oppure attraverso un processo meccanico, passando il filo in rulli a diversa velocità. Solitamente i fili usati per i TNT vengono stirati ad aria e successivamente raffreddati.
L’interlacciatura
A questo punto le fibre sia discontinue sia continue (sotto forma di rete bidimensionale, detta web, o tridimensionale, detta batt) vengono depositate su un tappeto aspirato e sottoposte a una lavorazione che gli permette di mantenere la coesione e la stabilità dimensionale. In ogni caso bisogna tenere presente che nessun TNT avrà le stesse resistenze meccaniche di un tessuto o di una maglia.
Esistono diverse tecniche per interlacciare le fibre. L’agugliatura in inglese è detta needlepunching, letteralmente “punzonatura ad ago”: sono infatti aghi in metallo a interlacciare le fibre in modo da renderle più stabili dimensionalmente (in modo unidirezionale o multidimensionale, o ancora in modo da creare texture particolari). È una tecnica usata spesso con TNT prodotti tramite dry-laid. Lo spunlace o hydroentanglement, letteralmente “intreccio ad acqua”, è una tecnica di interlacciatura simile all’agugliatura, ma in questo caso gli aghi sono sottilissimi ma potenti getti – veri e propri aghi – d’acqua. Più delicata dell’agugliatura tradizionale, non rovina le fibre tessili. Il termobonding e il through-air bonding sono tecniche che usano il calore per stabilizzare le fibre: nel termobonding il calore è diretto, impresso tramite cilindri riscaldati e puntinati; nel through-air bonding è indiretto, trasmesso tramite getti di aria calda. Le fibre possono essere coesionate anche con un procedimento chimico, attraverso sostanze adesive spruzzate, imbevute o cosparse sul tessuto e fissate con un passaggio in calandra o mangano. Un’altra tecnica consiste nella cucitura, con filo o senza: si chiama stitchbonding o maliwatt (dal tipo di telaio con cui viene prodotto il TNT). Un’ulteriore tecnica di coesionatura prevede infine l’uso di ultrasuoni.
Il finissaggio: bruciapelo e trattamenti superficiali
Su WIDE 44, nell’articolo dedicato al tessuto di poliestere, abbiamo detto che nel mondo tessile tutte le lavorazioni che servono a migliorare le caratteristiche di un tessuto vengono definite “finissaggio” (o “finitura”). Questo vale anche per il TNT, che viene trattato proprio come un tessuto vero e proprio.
Come possiamo immaginare, la superficie dei TNT non è particolarmente liscia e omogenea. Per eliminare i peli, i tessuti non tessuti possono passare in una macchina detta “bruciapelo”, che brucia la peluria con becchi a gas o sbarre arroventate.
Il TNT può anche subire trattamenti superficiali (bagni o spray) che ne migliorano determinate caratteristiche: idrorepellenza, resistenza al fuoco, resistenza agli acari, antibattericità… Rispetto agli additivi aggiunti in massa questi trattamenti sono meno resistenti e duraturi, perché non penetrano nella fibra. Lo stesso avviene per la tinta: se realizzata a questo punto del processo produttivo interessa solamente la parte superficiale dei fili. Le chimiche usate dipendono dai materiali di base.
Il tessuto non tessuto è uno dei grandi protagonisti di questi giorni di emergenza. Moltissimi dei dispositivi medico-sanitari e di protezione individuale (DPI) sono realizzati proprio con questo materiale: dai camici ai copricalzari usa e getta, realizzati in TNT accoppiato per garantire l’impermeabilità, dalle mascherine ai filtri usati per la purificazione dell’aria in aziende e ospedali. Sono molte le aziende legate al mondo della stampa (e non solo) che hanno iniziato a produrre materiale utile alla collettività. Hanno messo in campo competenze e creatività, e spesso hanno stretto partnership interessanti per riuscire a realizzare dispositivi di protezione utili e sicuri. Un modo bellissimo per prenderci cura di noi. Tutte le normative tecniche che fanno riferimento ai dispositivi necessari in queste settimane sono disponibili gratuitamente online sul sito dell’UNI (l’Ente Italiano di Normazione). Mascherine diverse da queste non sono dispositivi medici né dispositivi di protezione individuale. Possono essere comunque prodotte e vendute, ai sensi dell’art. 16, comma 2, del D.L. 18/2020, sotto la responsabilità dei produttori.
Altri finissaggi: accoppiatura, resinatura, coatizzazione, laminazione
Il TNT viene spesso usato insieme ad altri materiali: hanno un’anima in TNT, per esempio, i banner in PVC e le borse in pelle sintetica, ma anche i tubi di gomma. Proprio come i tessuti, anche i TNT possono subire diversi finissaggi. Possono essere accoppiati ad altri materiali, magari impermeabili. Possono essere “resinati” sul retro o “coatizzati” sul fronte, per aumentare la stampabilità ma conferire anche proprietà antisfilo, di resistenza al fuoco e idrorepellenza, resistenza all’acqua, protezione dai raggi UV e antimuffa. La coatizzazione modifica intensamente la natura del materiale: il TNT diventa di fatto un supporto per la resina, e passa (letteralmente) in secondo piano. La pelle sintetica spesso non è altro che TNT coatizzato, come abbiamo visto sul numero 47 di WIDE. Infine, i tessuti non tessuti possono essere laminati, cioè protetti con una lamina funzionale o decorativa, trasparente o colorata. La laminazione conferisce al materiale una perfetta impermeabilità, e per questo viene adottata per esempio nella produzione di dispositivi medici e dispositivi di protezione individuale (DPI).
La decorazione: stampa e goffratura
I TNT, ovviamente, possono essere anche decorati. A seconda del materiale di cui sono composti, delle loro caratteristiche fisiche e delle destinazioni d’uso dei prodotti finiti possono essere stampati con tecnologie analogiche oppure digitali.
Tra le tecnologie analogiche vengono usate la serigrafia, la flessografia, la stampa a rotocalco. Anche il getto d’inchiostro viene usato spesso: eco-solvent, latex, UV e UV-LED (magari con pretrattamenti specifici per migliorare l’adesione degli inchiostri). Nel caso in cui il TNT sia di poliestere (e quindi sopporti le temperature necessarie per il passaggio in calandra) è particolarmente diffusa la stampa a sublimazione, soprattutto indiretta: il fatto di non dover stampare direttamente la superficie irregolare e pelosa del tessuto non tessuto minimizza i rischi per le testine.
Quando si stampa il TNT si devono usare alcune accortezze, come fare delle prove per valutare l’eventuale restringimento longitudinale e trasversale in seguito all’asciugatura o al passaggio in calandra. Le prove di stampa servono anche a controllare la resa dei colori ed eventuali viraggi dovuti alle sostanze usate nel processo di fabbricazione del materiale. Sono elementi potenzialmente critici, e quindi da tenere in considerazione, anche la finezza e la planarità del tessuto.
Un’altra lavorazione alla quale può essere sottoposto il TNT è la goffratura, realizzata con una calandra in acciaio che incide una decorazione lineare. Con la nobilitazione di stampa e goffratura anche un materiale “umile” come il TNT può così ricoprire un ruolo da protagonista in un mercato esigente come quello della comunicazione visiva.
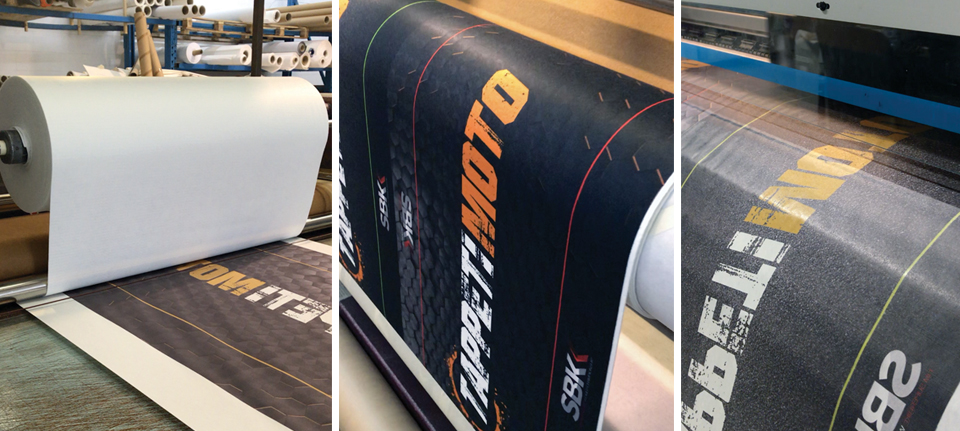
Nel processo di stampa a sublimazione indiretta la carta transfer viene accoppiata al TNT in poliestere e poi passata in calandra per trasferire l’inchiostro. Foto: Sublilife
Abbiamo intervistato i titolari di due aziende specializzate nella stampa digitale su TNT: ci siamo fatti raccontare la loro esperienza nel settore e nella gestione di questo materiale.
- Cosa producete in TNT?
- Con quali tecnologie di stampa?
- Chi sono i vostri clienti?
- Da quanto tempo lavorate nella stampa digitale?
Mauro Balossi (AD, Sublylife)
1 – Siamo specializzati nella produzione di tappeti sottomoto realizzati in TNT di poliestere e gommati. Un prodotto molto di nicchia, ma necessario per legge, per ragioni di sicurezza e di tutela ambientale, in tutte le gare di motociclismo.
2 – Siamo specializzati nella stampa transfer in sublimazione: trattiamo solamente il poliestere, anche nelle sue forme più difficili da stampare, come moquette e tappeti.
3 – I nostri clienti principali sono aziende che lavorano nel mondo degli eventi e degli allestimenti.
4 – Lavoriamo nel settore della stampa digitale da circa vent’anni: abbiamo puntato su questa tecnologia quando erano ancora in pochi a crederci. Sono un curioso: all’epoca mi aveva affascinato il digitale, avevo voluto subito sperimentare e sono stato tra i primi ad acquistare un plotter per la sublimazione. Nel tempo ho stampato con questa tecnica un po’ di tutto, materiali rigidi e flessibili.
Giancarlo Miotto (AD, TicTac Stampa)
1 – Abbiamo un focus particolare nel settore sportivo, che conosco bene. Produciamo principalmente banner, a pezzo o in bobina; “segnapercorso” per eventi sportivi, bobine lunghe anche 1.000 metri e alte 8 centimetri che servono a delimitare il percorso di gara; pettorali, che realizziamo interamente in azienda; copritransenne.
2 – Siamo sempre alla ricerca delle soluzioni più sostenibili e originali: abbiamo fatto sviluppare in esclusiva degli inchiostri fluo (giallo e fucsia) per la nostra macchina a sublimazione, e abbiamo studiato una speciale combinazione di primer e inchiostri green che usiamo su una stampante UV.
3 – Organizzatori di eventi, soprattutto sportivi, e allestitori.
4 – È dal 1996 che stampiamo in digitale, e le prime prove di stampa su TNT risalgono al 1998 circa: praticamente dei pionieri. Oggi stampiamo ogni tipo di materiale di grande formato, e ci siamo specializzati anche nella finitura (taglio, fustellatura, occhiellatura).