La stampa 3D nel settore manifatturiero attraverso lo sguardo di chi la usa tutti i giorni
La stampa 3D è uno dei temi più caldi degli ultimi anni, capace non solo di essere sulla bocca di tutti ma anche di farsi prepotentemente largo nelle principali fiere di settore – basti pensare al peso avuto nell’ultima drupa per averne un’idea. D’altro canto, qual è l’effettivo impatto del 3D printing, al netto della vox populi e del clamore che l’argomento suscita? Si appresta davvero a cambiare completamente il volto della produzione di beni di consumo? Siamo veramente vicini al momento in cui quasi ogni cosa attorno a noi sarà stata stampata in 3D? Oppure questa tecnologia è destinata a rimanere limitata in alcuni settori di nicchia e nella prototipazione? Una recentissima ricerca – condotta nell’ottobre 2017 dall’ente di ricerca indipendente Dimensional Research su mandato di Jabil, società americana fornitrice di servizi per il settore manifatturiero – fornisce un quadro pratico del segmento attraverso le risposte di oltre 300 decision maker e utilizzatori di aziende attive nella produzione di beni di consumo.
Produzione o test?
Il primo dato che emerge è che la tecnologia di stampa additiva è ben presente nelle aziende manifatturiere: l’81% la utilizza quotidianamente, in particolare in campo aerospaziale e medicale (93% e 91% rispettivamente). La percentuale di adozione è proporzionale alle dimensioni della società: la quasi totalità delle aziende con più di mille dipendenti l’ha già adottata (92%) mentre poco più della metà di quelle con meno di 100 impiegati ha fatto analoga scelta (60%). Tuttavia, questa diffusa presenza è molto spesso dovuta a un utilizzo per la prototipazione (70% dei rispondenti). Solo il 36% utilizza il 3D su tutto l’arco produttivo, il 33% per la realizzazione di attrezzature, il 28% per la prima fase della produzione e unicamente il 16% ne fa uso per le riparazioni e la creazione di parti di ricambio. Non è un caso che, domandando da dove parta la richiesta di adozione del 3D printing, il 70% degli intervistati abbia indicato i reparti di R&D come principali sponsor – ovvero coloro che, responsabili delle innovazioni di prodotto, maggiormente utilizzano la prototipazione per testare rapidamente ciò che stanno sviluppando. Un segnale comunque interessante viene dal fatto che il 50% delle volte anche la produzione è interessata alla tecnologia additiva, indice che comunque la stampa 3D si sta facendo largo anche fuori dai laboratori di R&D.
Materiali
Esattamente come per il resto del mondo della stampa, quello dei materiali è un argomento particolarmente rilevante. La versatilità di supporti è sempre più richiesta e negli ultimi anni il 3D printing ha fatto notevoli passi in avanti, affiancando ai materiali plastici sempre nuove possibilità tra cui metalli, ceramiche e composti. Tuttavia, la plastica continua a regnare sovrana – la sceglie l’81% dei rispondenti – e solamente un terzo utilizza metalli e ceramiche (34% e 32% rispettivamente). I materiali composti sono a oggi molto di nicchia, con solo l’8% che ne fa uso. Tali percentuali sono direttamente correlate all’utilizzo che viene fatto della stampa 3D e ai settori in cui è maggiormente adottata. Come detto, medicale e aerospaziale sono ai primi posti, seguiti dall’automotive, dall’elettronica e produttori di attrezzature. Analizzando questi cinque settori di mercato, si vede che in nessuno di essi la stampa 3D è primariamente usata per la produzione. Tuttavia, ci sono delle differenze sostanziali: il 41% di ciò che viene stampato in 3D nel medicale è un prodotto finito, contro il 29% dell’elettronica e il 19% dell’automotive. Che, girato, implica un 81% di prototipazione in quest’ultimo segmento. Essendo i materiali plastici quelli più facili da reperire, presenti sul mercato da più tempo e pertanto maggiormente affidabili, il loro dominio non è una sorpresa, semplicemente è il risultato dell’utilizzo che viene fatto della tecnologia additiva.
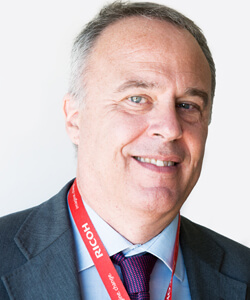
Giorgio Bavuso, direttore Commercial and Industrial Printing di Ricoh Italia
Abbiamo parlato con Giorgio Bavuso, direttore Commercial and Industrial Printing di Ricoh Italia, per fare il punto della situazione a due anni dall’ingresso dell’azienda nel mondo della stampa 3D.
Come avete scelto di entrare nella stampa 3D?
Abbiamo puntato su un sistema proprietario – Ricoh AM S5500P – per poter dare al mercato una versatilità applicativa a 360°, che spazia dalla prototipazione alla realizzazione di parti finite. Non a caso abbiamo scelto un volume di costruzione ampio – (L) 550 mm x (P) 550 mm x (A) 500 mm – che consente di produrre oggetti di grandi dimensioni, evitando così il postassemblaggio dei componenti, oppure di realizzare varie parti nel corso di un’unica lavorazione. Anche a livello di materiali vogliamo essere il più flessibili e ampi possibili, coprendo tutta la gamma di materiali plastici, per poterci rivolgere a molteplici settori industriali, dall’automotive all’aerospaziale.
Che risposte avete avuto dal mercato? Come vi state muovendo?
Il nostro business della stampa 3D è ancora giovane, ma abbiamo già ricevuto reazioni molto positive. Stiamo costruendo una forte presenza in diversi mercati chiave e continueremo a espanderci. Inoltre, collaboriamo costantemente con partner e clienti per mettere a fattor comune le varie competenze e sviluppare nuove possibilità. Stiamo lavorando per accrescere sempre più le nostre competenze in termini di materiali e ottimizzare la nostra presenza in questo settore. A formnext 2017 abbiamo presentato la tecnologia Binderjet, che utilizza come materiali di stampa metalli, alluminio, titano e magnetite.
Impatto
A questo punto, appurato che difficilmente nei prossimi mesi l’industria manifatturiera verrà completamente sovvertita dalla stampa 3D, bisogna interrogarsi sull’effettivo impatto di questa tecnologia sul mercato. Un cambiamento di paradigma è in atto, la quasi totalità dei rispondenti ne è convinta (91%, per l’esattezza). Il 36% ritiene che questo cambio stia già modificando il modo di pensare e lavorare, il restante 55% rimane più prudente ma comunque sicuro che avverrà. Questa trasformazione conduce necessariamente a un impiego molto più diffuso della stampa 3D nella produzione vera e propria nei prossimi anni: solo il 7% afferma che il proprio utilizzo non muterà, per il 36% aumenterà, per il 38% raddoppierà e per il 19% addirittura si quintuplicherà. Un’altra dinamica su cui la stampa 3D va a influire è quella della produzione locale, sia nella riduzione dei tempi di consegna, sia nella possibilità di “riportare a casa” quelle lavorazioni che oggi vengono realizzate all’estero perché più vantaggiose in termini economici. Secondo il 24% del campione, la stampa additiva avrà certamente quest’ultimo effetto, mentre il 60% ritiene che potrebbe averlo e il 16% che le cose non cambieranno rispetto a come sono oggi. Interessante notare come queste percentuali variano significativamente a seconda dell’area geografica: gli americani sono i più ottimisti (27%, 61%, 11%), l’Asia Pacific è decisamente più prudente (4%, 61%, 35%) mentre in EMEA il 41% ritiene che il 3D non cambierà le cose (6% e 53% le altre due opzioni).
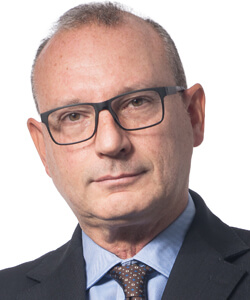
Davide Ferrulli, enterprise sales manager 3D Printing Business di HP Italy
Il connubio tra stampa 3D e settore manifatturiero esiste da anni, ma una serie di ostacoli ha finora impedito a questa tecnologia di giocare un ruolo da protagonista. Ruolo che invece intende ritagliarsi HP, entrata nel settore con un sistema proprio. Ne abbiamo parlato con Davide Ferrulli, enterprise sales manager 3D Printing Business di HP Italy.
Siete entrati da poco tempo nel mondo della stampa 3D. Qual è la visione che vi ha condotto a questo passo?
Quello della stampa 3D, a dispetto del fatto che la tecnologia sia nata decenni orsono, è un mercato che è cresciuto poco nel corso del tempo, in particolare perché la stampa additiva viene utilizzata principalmente per la prototipazione e non per la produzione vera e propria. Fra le cause di ciò ci sono le basse velocità di lavorazione e il numero di pezzi che è possibile produrre, del tutto dissimile da quello ottenibile con le tecnologie industriali tradizionali. Senza considerare che la stampa 3D a singolo pezzo costa di più. Non a caso, i settori nei quali è maggiormente affermata sono anche quelli dove la richiesta di grandi quantità di pezzi è molto bassa. HP ha deciso pertanto di lavorare con una tecnologia nuova, dato che quelle esistenti rendevano impossibile superare questi ostacoli alla crescita. Per risolvere il problema della velocità abbiamo abbandonato la stampa spot per adottare un approccio che permettesse di stampare l’intero livello in un colpo solo – un po’ come passare, nel 2D printing, dalla stampa a aghi a quella laser. L’altro aspetto su cui abbiamo lavorato è quello del costo pezzo. Ad oggi, la regola è che chi produce la macchina produce anche i materiali e uno specifico modello funziona solo con uno specifico materiale. HP ha deciso di puntare su un modello alternativo, creando una piattaforma aperta per i materiali con cui generare una competizione che, sull’esempio di altri settori, vuole abbassare il prezzo del materiali a un livello finora sconosciuto a questo mercato.
A quali settori vi rivolgete principalmente?
Un target è rappresentato da chi necessita di elevata produttività, ovvero dai centri stampa 3D che devono rispondere a molteplici richieste con tempi di lavorazione e di consegna sincopati. Parallelamente, ci sono molte realtà che producono componenti plastici (da qualche centinaio a qualche migliaio di pezzi) e che hanno bisogno di sistemi con costi contenuti – cosa che i sistemi tradizionali non possono assicurare. In entrambi i segmenti abbiamo riscontrato un notevole interesse, in particolare presso aziende che avevano interesse per la stampa 3D ma questa non era per loro immediatamente adottabile a causa delle limitazioni sopracitate.
Quali sono le problematiche che riscontrate sul mercato e quale risposta state avendo?
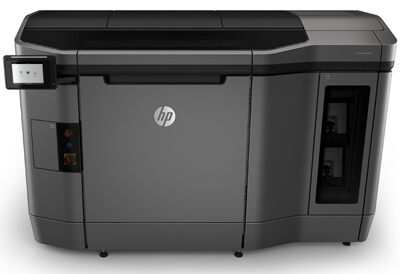
HP Jet Fusion 3D è la soluzione di HP per la stampa additiva, disponibile in tre differenti modelli
Siamo sulla buona strada, ma certamente c’è ancora parecchio da lavorare. Anzitutto sulle competenze: ci sono tante aziende che, pur avendo adottato la stampa 3D, la sfruttano al di sotto delle sue possibilità perché continuano a utilizzare progetti che non sono stati creati ad hoc, ma che sono gli stessi utilizzati con tecnologie tradizionali. Pensare ai prodotti avendo già presente che verranno realizzati tramite stampa 3D, invece, permette di eliminare tutte quelle correzioni di adattamento finora necessarie. Anche la supply chain viene interessata dalla stampa 3D: si tende a passare da un modello di spedizione fisica (con conseguente necessità di magazzino, costi di trasporto, …) a uno in cui vengono spediti dati a una stampante che si trova all’altro lato del mondo, andando a produrre solo quel che serve e solo dove serve. Proprio per questo motivo HP sta lavorando a una serie di partnership che possano dare ai clienti gli strumenti consulenziali e non per affrontare al meglio questi cambiamenti. Che non sono semplice teoria, ma qualcosa già in atto. Ci sono parecchie aziende che hanno ufficialmente annunciato uno spostamento di parte della loro produzione dai sistemi tradizionali a quelli 3D. Abbiamo non pochi clienti che non solo hanno deciso di scommettere sulla nostra tecnologia, ma che hanno già confermato la bontà della loro scelta ampliando il parco macchine con nuove installazioni. E questo dopo pochi mesi. Dal nostro punto di vista questa è la riprova che la strada intrapresa è quella giusta.
Benefici e sfide
Diamo ora uno sguardo agli aspetti più interessanti della tecnologia 3D e alle principali problematiche che le aziende affrontano nel suo utilizzo. Ovviamente, variano da settore a settore: un’azienda attiva nell’aerospaziale avrà maggiori benefici da innovazioni nel design e nelle performance del prodotto e, di conseguenza, realizzare pezzi qualitativamente validi sarà una delle sue principali sfide; una società di automotive, invece, potrebbe essere maggiormente interessata alla riduzione di costi offerta dalla stampa 3D e, pertanto, vedere in tutti i costi esterni al processo di produzione vero e proprio un problema di grande rilievo. Tuttavia, è comunque possibile stilare delle classifiche generiche. Parlando di benefici, al primo posto spiccano la rapidità nel portare sul mercato nuove idee e l’innovazione di design e performance (52%), seguite a ruota dalla velocità di produzione (50%) e dalle possibilità di personalizzazione (48%). Libertà di design e riduzione dei costi sono vantaggi significativi per poco più del 40% del campione, mentre la riduzione del magazzino e la produzione di parti di ricambio sono decisamente meno rilevanti (27% e 23% rispettivamente). Unicamente il 3% ha affermato che la stampa 3D è solo una tecnologia alternativa senza particolari vantaggi. L’altro lato della medaglia è rappresentato dalle sfide quotidiane che le aziende devono affrontare. Al di là di un 4% che non ha incontrato problemi di sorta, per tutti gli altri la principale criticità è la mancanza di esperienza (43%) e quindi l’impossibilità di usare immediatamente tutte le potenzialità della tecnologia 3D. Anche i costi iniziali sono ritenuti un ostacolo non indifferente (39%), così come quelli dei materiali (34%). Dopo questo trittico, la classifica delle problematiche vede aspetti più tecnici: anzitutto la qualità dei prodotti realizzati, che per il 33% è un tema sensibile; poi le limitazioni nei materiali (29%) e nelle possibilità tecnologiche generali della manifattura additiva (26%); infine la difficoltà nel ridimensionamento (22%, problema particolarmente sentito in ambito medicale e aerospaziale) e, come fanalino di coda, i costi esterni alla fase di produzione (17%). Preso atto dei problemi riservati dalla stampa 3D, praticamente tutti i rispondenti sono convinti che questi possano essere superati. Per riuscirci, sono necessari aggiornamento del personale esistente e/o assunzione di personale qualificato (57%), nuovi investimenti da parte dell’azienda (52%), un cambio interno di mentalità con conseguente tempo di adattamento (48%), innovazioni tecnologiche (47%). Oltre la metà del campione ritiene che queste sfide verranno superate entro i prossimi tre anni al massimo, mentre un ulteriore 32% guarda ai cinque anni come tempo necessario.
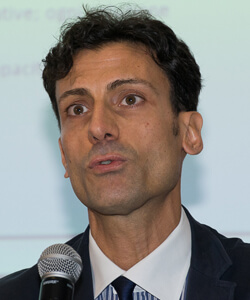
Marco Marcuccio, sales manager di CMF Marelli
Rappresentante italiano di marchi storici quali 3D Systems, CMF Marelli vanta una lunga storia nel settore della stampa 3D – o più propriamente additive manufacturing. Forte di questo punto di vista privilegiato, abbiamo chiesto a Marco Marcuccio, sales manager di CMF Marelli, un’opinione sul mercato e i suoi trend.
Quali sono i principali trend a livello industriale? Come si posiziona l’Italia rispetto al resto d’Europa?
Negli ultimi tempi – dopo che il mercato consumer è esploso per poi ridimensionarsi con eguale rapidità – il mercato del 3D è tornato a focalizzarsi sui segmenti di/a maggior valore aggiunto: prototipazione professionale e produzione industriale. In quest’ultimo comparto, i trend più significativi sono principalmente due: innovazione tecnologica e materiali. La sinterizzazione classica di polveri in plastica o lega viene progressivamente affiancata da nuove tecnologie che si stanno dimostrando più accessibili e produttive: fra queste ricordiamo CFF per la deposizione continua di fibre e ADAM per l’estrusione del metallo. Al contempo, sempre nuovi materiali stanno facendo la loro comparsa: carbonio e kevlar, ad esempio, si stanno dimostrando molto performanti e adatti a realizzare prodotti finali che sono equiparabili, se non migliori, delle controparti ottenute con processi tradizionali. Accanto a ciò, è significativo sottolineare come nuovi player, soprattutto grandi aziende attive nella stampa 2D, hanno iniziato a presentare le proprie proposte attratti dalle dinamiche e dalla prospettive di queste opportunità laterali. Queste dinamiche, geograficamente parlando, sono guidate dall’Europa, al cui interno l’Italia resta uno dei mercati più significativi.
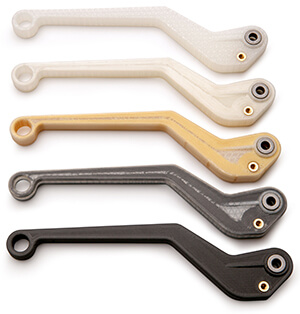
Alcuni esempi di parti stampate in 3D
Focalizzandoci sul mercato nazionale, come vi state muovendo per ampliare la gamma di materiali e possibilità cromatiche della stampa 3D?
Come accennato, il mercato richiede e apprezza una scelta sempre maggiore di consumabili e una combinazione tecnologia/macchina che garantisca l’uso di materiali con proprietà meccaniche superiori. Ad esempio, nella nostra qualità di rivenditori di Markforged possiamo offrire al mercato sia stampanti che permettono di costruire oggetti in materiali compositi plastici rinforzati con fibra a deposizione continua; sia porre sul mercato l’ultimissima nata della casa di Boston, un sistema per costruire in metallo (acciaio, alluminio, titanio ecc.) in maniera molto economica. Si tratta di sistemi che hanno un forte impatto in svariati segmenti quali l’aerospaziale, il meccanico, l’automotive. Rispetto al passato, invece, è da notare una minore richiesta di stampanti in full-colour. Questo non perché la tecnologia sia intrinsecamente meno valida, ma perché viene utilizzata per prodotti che sono più estetici che funzionali e i settori di utilizzo – l’architettonico, il didatticomuseale, il calzaturiero, la rubinetteria – stanno dimostrando di avere budget minori da dedicare a queste tipologie di investimenti.
L’importante è (non) essere primo
Concludiamo con un aspetto decisamente curioso ma rilevante: le aziende manifatturiere guardano alla stampa 3D, ne analizzano benefici e problemi, ma sono ben pochi quelli che desiderano fare gli apripista. Solo il 12% è animato da spirito pionieristico, sono molti di più quelli che sono pronti a fare rapidamente certi passi dopo aver visto che funzionano (67%). Un altro 18% è invece ancor più drastico: solo dopo che la stampa 3D sarà la tecnologia standard del settore, allora vi entreranno. Tirando le fila, si può affermare che la stampa 3D sta penetrando nel settore manifatturiero con dinamiche che lo cambieranno in profondità, ma che questi mutamenti non sono necessariamente immediati. C’è un diffuso interesse che però va di pari passo con un atteggiamento complessivamente prudente e ci vorranno alcuni anni prima che aspetti che ora inibiscono un’adozione più massiccia in fase produttiva vengano definitivamente superati.